A conformidade das barras e perfis de cobre para aplicações elétricas
Redação
Da fiação elétrica doméstica comum às hélices de barco e das células fotovoltaicas aos saxofones, o cobre e suas ligas são empregados em uma infinidade de usos finais. De fato, o uso do metal em uma ampla gama de indústrias principais resultou na comunidade de investimentos se voltando para os preços do cobre como um indicador da saúde econômica geral. Para entender melhor as várias aplicações do cobre, os especialistas classificaram quatro setores de uso final: elétrico, construção, transporte e outros. A porcentagem da produção global de cobre consumida por cada setor é estimada em elétrica: 65%; construção: 25%, transporte: 7% e outros: 3%. Deve-se conhecer os requisitos para barras e perfis de cobre para aplicações elétricas.
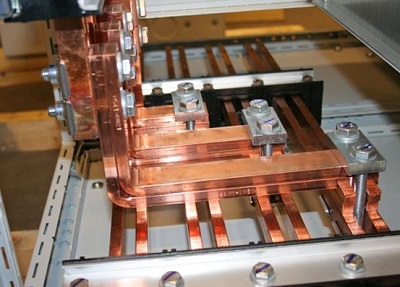
Da Redação –
Além da prata, o cobre é o condutor mais eficaz de eletricidade . Isso, combinado com sua resistência à corrosão, ductilidade, maleabilidade e capacidade de trabalhar em uma ampla gama de redes de energia, torna o metal ideal para a fiação elétrica. Praticamente toda a fiação elétrica, exceto as linhas aéreas (feitas de alumínio mais leve), são formadas com cobre.
Barramentos, condutores que distribuem energia, transformadores e enrolamentos de motores também dependem da condutividade do cobre. Devido à sua eficácia como condutor de eletricidade, os transformadores de cobre podem ter uma eficiência de até 99,75%.
Aplicações elétricas, incluindo tecnologia de computador, televisores, telefones celulares e dispositivos eletrônicos portáteis, nas últimas décadas se tornaram um grande consumidor de cobre. Dentro desses dispositivos, o cobre é vital para a produção de: conectores eletrônicos, fiação e contatos do circuito, placas de circuito impresso, microp...