Os ensaios em tubos de aço de grande diâmetro
Redação
Um tubo é uma seção tubular ou um cilindro oco, geralmente mas não necessariamente de seção circular, usado principalmente para transportar produtos de um local para outro. Os produtos devem permitir a fluição de líquidos e gases (fluidos), pastas, pós e massas de pequenos sólidos. Eles devem ser fabricados de acordo com os requisitos e os métodos de ensaio no fornecimento de tubos de aço com solda de diâmetro nominal (externo) igual ou maior que 457 mm (18”).
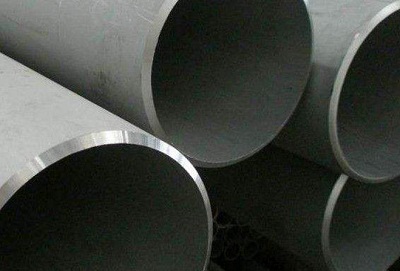
Da Redação –
Os tubos são dutos fechados destinados ao transporte de fluidos e geralmente são de seção circular. Conduto forçado, sem superfície livre. O termo usado para denominar um conjunto de tubos e seus acessórios é tubulação ou sistema de escoamento. Se for necessário, os tubos podem ter acabamento mais liso (sanitário) que os de fabricação padrão. Os tubos geralmente são definidos pelo diâmetro externo e a espessura da parede é de 1,5 mm para todos os diâmetros disponíveis no mercado, com exceção do tubo de 4".
Os tubos podem ser fabricados com muitos tipos de materiais, incluindo metais, ligas, cerâmica, vidro, fibra de vidro, concreto e plástico. As empresas possuem engenheiros de materiais para determinar os materiais a serem utilizados nos sistemas de tubulação de processos.
A seleção de material é baseada principalmente no serviço de fluido, pressão do projeto, temperatura e custo do projeto, com mais algumas considerações. Segundo os materiais, a maioria dos tubos...