A confiabilidade e a manutenção dos ativos industriais
Redação
A manutenção dos ativos deve evoluir à medida que o mercado se torna cada vez mais competitivo.
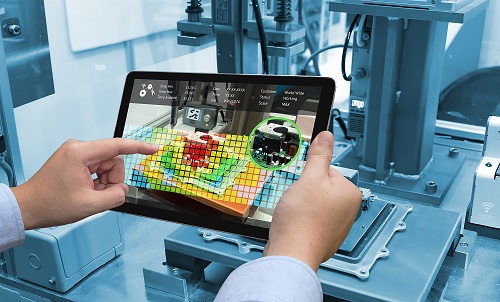
Cristiano Bertulucci Silveira -
A confiabilidade e a manutenção dos ativos industriais tornaram-se tão importantes quanto qualquer outra disciplina de gerenciamento. Isto se deve ao fato de que a crescente mecanização e a automatização dos processos geraram uma forte dependência do ser humano por estes sistemas.
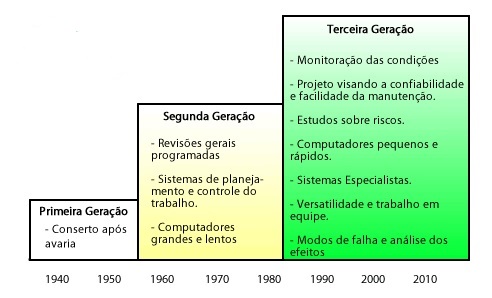
Em qual geração sua empresa se encontra?
O motivo não foi somente porque a falha deles acarretava em perdas produtivas, mas porque muitas vezes a falha poderia gerar acidentes fatais. Como exemplo, podemos citar uma falha em um motor de um avião em pleno voo acarretando em um grave acidente.
Com o ligeiro crescimento do volume de produção nas indústrias, ocasionado principalmente pelo desenvolvimento tecnológico, as empresas aumentaram a capacidade de geração de receita vendendo mais seus produtos e gerando cada vez mais lucro. A necessidade de manter este cenário constante começou a ser de fundamental importância para a sobrevivência do negócio e a confiabilidade operacional dos equipamentos passou a ser tratada de forma estratégica.
É sabido que cada vez que a linha produtiva é parada, a empresa deixa de ter um ganho razoável que tinha direito, por culpa ou inexecução de seus ativos. Chamamos isto de lucro cessante.
Além do lucro cessan...