Metodologia simplificada de cálculo do rendimento térmico de caldeiras
Redação
Define-se rendimento térmico de uma caldeira como sendo a fração da potência liberada na câmara de combustão que é transferida ao fluido de trabalho. Não havendo metodologia normalizada no Brasil para o cálculo do rendimento de caldeiras, costuma-se utilizar normas de outros países. A metodologia de cálculo desenvolvida pelo Laboratório de Engenharia Térmica (LET) do IPT é baseada nas normas dos Estados Unidos (ASME) e Alemanha (DIN), e vem sendo utilizada em trabalhos realizados para a indústria envolvendo o uso eficiente de combustível.
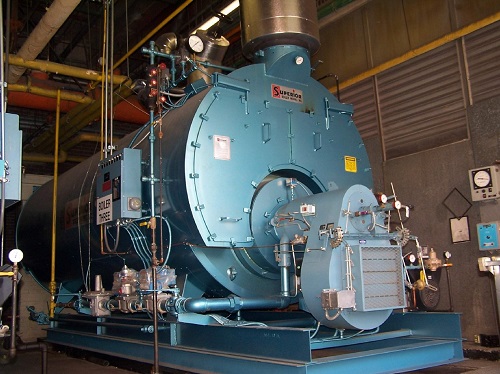
Renato Vergnhanini Filho -
As caldeiras são equipamentos comumente encontrados na indústria para a geração de vapor, seja para aquecimento, seja para a geração de energia elétrica. No caso mais comum, a caldeira é um trocador de calor onde há a transferência de calor dos gases quentes - produzidos pela queima de um combustível - para a água. A água, ao receber calor, aquece-se e vaporiza-se, daí o nome “caldeira de vapor”,
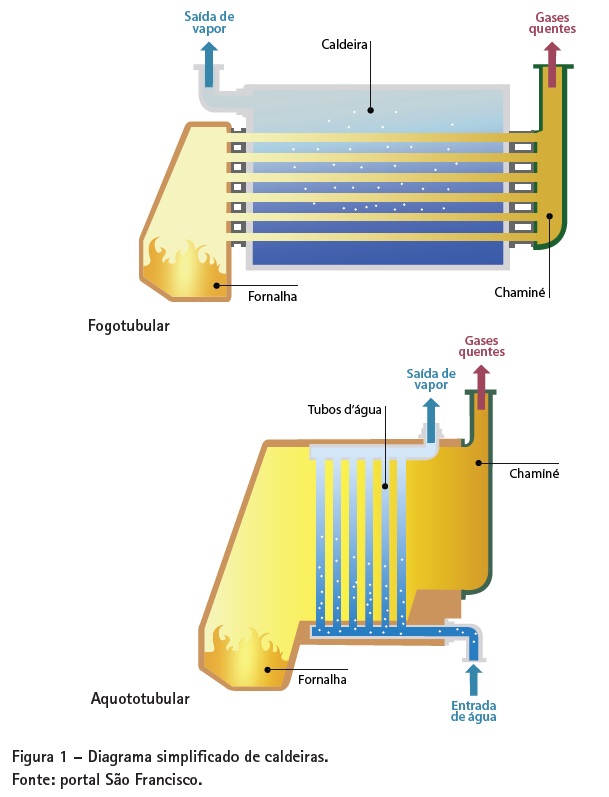
Na operação das caldeiras, por questões financeiras, ambientais ou estratégicas, é cada vez mais importante a preocupação com a eficiência energética, sendo o cálculo do seu rendimento térmico a forma de avaliação comumente utilizada. De maneira simplista, define-se rendimento térmico, ou eficiência térmica, de uma caldeira como sendo a fração da potência liberada na câmara de combustão que é transferida ao fluido de trabalho (água - vapor).
Não há metodologia normalizada no Brasil para o cálculo do rendimento de caldeiras. Costuma-se utilizar normas de outros países, geralmente dos Estados Unidos (American Society of Mechanical Engineers, 1999) ou da Alemanha (Deutsches Institut für Normung E.V., 1996), que serão designadas neste texto simplesmente por “norma ASME” e “norma DIN”, respectivamente.
Dentro desse contexto, o LET desenvolveu metodologia simplificada para o...