A Qualidade em uma fábrica inteligente
Redação
As fábricas aparentemente burras no passado começaram a ficar inteligentes e a tomar muitas decisões por conta própria.
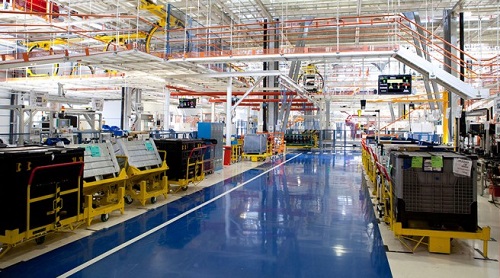
Nikhil Padhi e Prasanna Kumar Illa -
Nas últimas décadas, as fábricas evoluíram continuamente. Elas se tornaram um modo de vida com a Revolução Industrial, criando empregos e, muitas vezes, um município em torno deles.
As décadas de 1970 e 1980 viram a adoção de conceitos inovadores de manufatura, como just in time e total quality management. Também viu o surgimento da automação industrial e dos robôs, que mudaram a cara da manufatura. O centro de gravidade no mundo da manufatura passou do trabalho para a tecnologia.
E isso foi apenas o começo: as fábricas logo começaram a ser entidades voltadas para dados. Elas começaram a aproveitar enormes volumes inexplorados de dados gerados no chão de fábrica que, de outra forma, passavam despercebidos. As fábricas aparentemente burras começaram a ficar inteligentes e a tomar muitas decisões por conta própria.
Essas fábricas inteligentes simbolizam o santo graal da manufatura. Toda organização está tentando superar a próxima quando se trata de construir fábricas inteligentes. No entanto, um dos objetivos fundamentais da manufatura é fabricar produtos...