Os testes de conformidade dos sistemas de automação industriais
Redação
A automação industrial é o uso de sistemas de controle, como computadores ou robôs, e tecnologias da informação para lidar com diferentes processos e máquinas em uma indústria para substituir um ser humano. É o segundo passo além da mecanização no âmbito da industrialização. Esses sistemas passam por testes de aceitação em fábrica (TAF), testes de aceitação em campo (TAC) e os testes de integração em campo (TIC) para demonstrar que o sistema de automação está de acordo com as especificações técnicas.
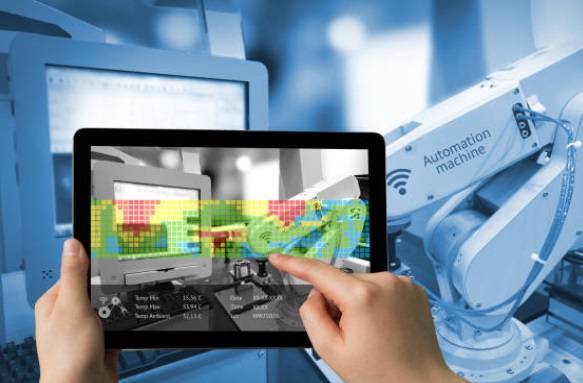
Da Redação –
No seu início, o objetivo da automação era aumentar a produtividade, pois os sistemas automatizados podem funcionar 24 horas por dia e reduzir o custo associado dos operadores humanos, ou seja, os salários e os benefícios). No entanto, hoje, o foco da automação mudou para aumentar a qualidade e a flexibilidade em um processo de fabricação.
Na indústria automobilística, a instalação de pistões no motor era realizada manualmente, com uma taxa de erro entre a 1% a 1,5%. Atualmente, essa tarefa é executada usando máquinas automatizadas com uma taxa de erro de 0,00001%. Assim, essa tecnologia vem ofertando menor custo operacional, pois a automação industrial elimina os custos com assistência médica e férias remuneradas associadas a um operador humano.
Além disso, não exige outros benefícios aos funcionários, como bônus, cobertura de pensão, seguro, etc. Acima de tudo, embora esteja associada a um alto custo inicial, economiza os salários mensais dos trabalhado...