Flexibilizando e nivelando a produção com o heijunka
Redação
Heijunka é o ato de nivelar a variedade ou o volume de itens produzidos em um processo ao longo de um período de tempo. É um conceito que está relacionado à programação da produção e é a principal ferramenta aplicada para gerar estabilidade na produção.
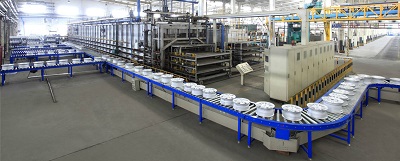
Cristiano Bertulucci Silveira -
Heijunka é o ato de nivelar a variedade ou o volume de itens produzidos em um processo ao longo de um período de tempo. É um conceito que está relacionado à programação da produção e é a principal ferramenta aplicada para gerar estabilidade na produção. Ele é utilizado para prevenir o excesso de lotes, tipos de produtos e flutuações no volume dos produtos. “A tartaruga é mais lenta, mas consistente. Causa menos desperdício e é muito mais desejável do que a lebre veloz que corre à frente e depois para, ocasionalmente, a cochilar. O Sistema Toyota de Produção pode ser realizado somente quando todos os trabalhadores se tornam tartarugas.” (Taiichi Ohno, 1988)
Atualmente muitas empresas tem como objetivo colocar em prática o lean manufacturing e produzir exatamente o que o cliente pede e quando ele pede. Todavia, o que acontece é que muitas empresas aceitam pedidos que oscilam de mês a mês.
Desta forma, é realizada a programação desigual da produção e isso acarreta em uma série de problemas que abrangem desde o pagamento de horas extras a funcionários até o estresse de...