A segurança das máquinas para trabalhar madeiras
Redação
No Brasil, o número de acidentes com máquinas ainda é bastante alto. Em todos os setores, como industrial, construção civil, agrícola, marceneiro, etc. Um desses setores, a indústria da madeira, apresenta muitos problemas relacionados a acidentes, falta de treinamentos adequados, falta de conscientização dos trabalhadores, etc. Quanto a esses fatores de ricos, as máquinas de cortar madeiras merecem bastante atenção.
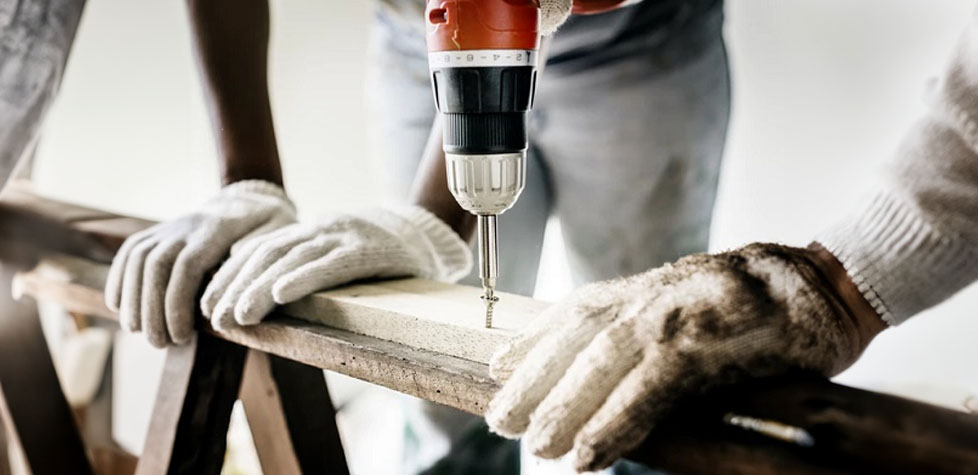
A carpintaria é o local onde trabalha o carpinteiro. Sua função é executar os mais diversos trabalhos em madeira, desde móveis e ferramentas até artigos para construção civil, dentre outros. É um trabalho que exige esforço físico e muitas vezes é realizado ao ar livre. Para ser um bom carpinteiro, é necessário que o trabalhador tenha noções de geometria e um amplo conhecimento de como lidar com a madeira no seu estado natural.
Já a marcenaria pode ser considerada uma evolução da carpintaria, pois o trabalhador lida mais com laminados industrializados, como compensado, aglomerado, MDF, folhas de madeira, etc. O marceneiro precisa ser criativo, saber desenhar e conhecer as ferramentas e materiais necessários para a realização do seu trabalho.
Nesses locais de trabalho, existem riscos para a saúde do trabalhador, devido à utilização de máquinas e equipamentos que oferecem um alto nível de perigo. É bastante comum encontrar trabalhadores operando com diversas máquinas ao mesmo tempo, colocando dessa forma, suas vidas em risco.
Dessa forma, para que o trabalho se transforme em algo seguro, é necessário que os trabalha...