A corrosão nossa de cada dia
Redação
A corrosão é um fenômeno químico que degrada o metal, chegando ao ponto de prejudicar, e muito, as suas propriedades mecânicas. Em trabalhos que envolvem o armazenamento e o uso de ferro e aço, é dever do projetista analisar o ambiente ao qual o metal será exposto, bem como o tempo de exposição. Em aspectos gerais, é mais vantajoso utilizar materiais resistentes ou métodos de proteção contra os efeitos adversos da atmosfera ou do local onde há o estoque. Muitas vezes, porém, devido principalmente a questões financeiras, são utilizados metais sem preparação, mesmo sabendo que ocorrerá a corrosão e a deterioração.
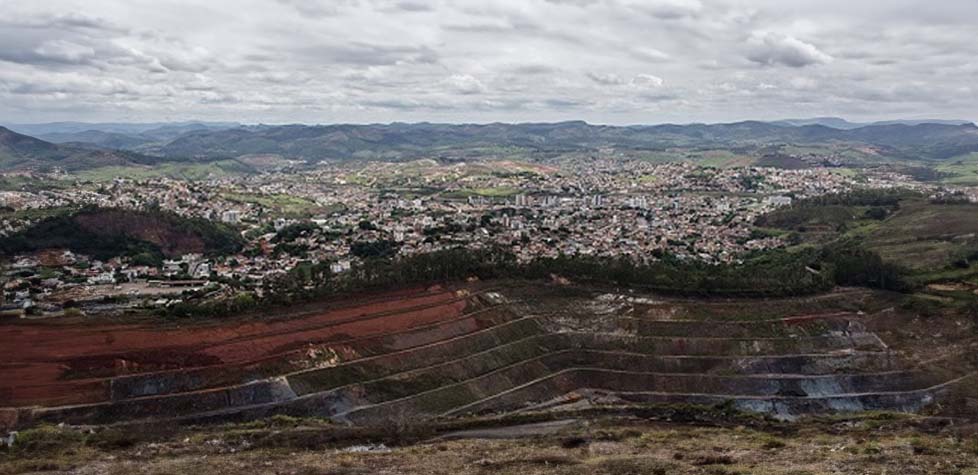
Confidência do itabirano
Carlos Drummond de Andrade
Alguns anos vivi em Itabira.
Principalmente nasci em Itabira.
Por isso sou triste, orgulhoso: de ferro.
Noventa por cento de ferro nas calçadas.
Oitenta por cento de ferro nas almas.
E esse alheamento do que na vida é porosidade e comunicação.
A vontade de amar, que me paralisa o trabalho,
vem de Itabira, de suas noites brancas, sem mulheres e sem horizontes.
E o hábito de sofrer, que tanto me diverte,
é doce herança itabirana.
De Itabira trouxe prendas diversas que ora te ofereço:
esta pedra de ferro, futuro aço do Brasil;
este São Benedito do velho santeiro Alfredo Duval;
este couro de anta, estendido no sofá da sala de visitas;
este orgulho, esta cabeça baixa…
Tive ouro, tive gado, tive fazendas.
Hoje sou funcionário público.
Itabira é apenas uma fotografia na parede.
Mas como dói!
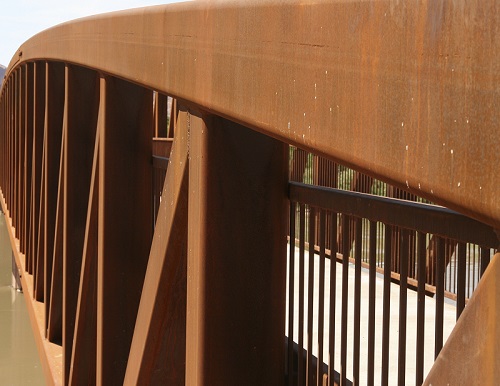
Hayrton Rodrigues do Prado Filho –
A corrosão é um processo de deterioração dos metais que resulta da interação entre agentes nat...