As descontinuidades em revestimentos anticorrosivos
Redação
Os revestimentos de proteção são uma maneira simples de reduzir a corrosão, limitando a exposição do metal a um ambiente corrosivo. A tinta é um revestimento protetor muito comum, mas também são usados alcatrão, piche, betume e plástico. Uma consideração importante para os revestimentos de proteção é garantir que o revestimento seja bem aderido ao metal e que ele permaneça intacto ou seja regularmente reparado/recoberto. Outra forma de revestimento protetor é colocar uma camada de outro metal na superfície do metal que você deseja proteger. Um tipo deste revestimento é conhecido como galvanização, onde o zinco é revestido em ferro ou aço. No caso da galvanização, o zinco atua como um ânodo e corrói preferencialmente o ferro ou o aço.
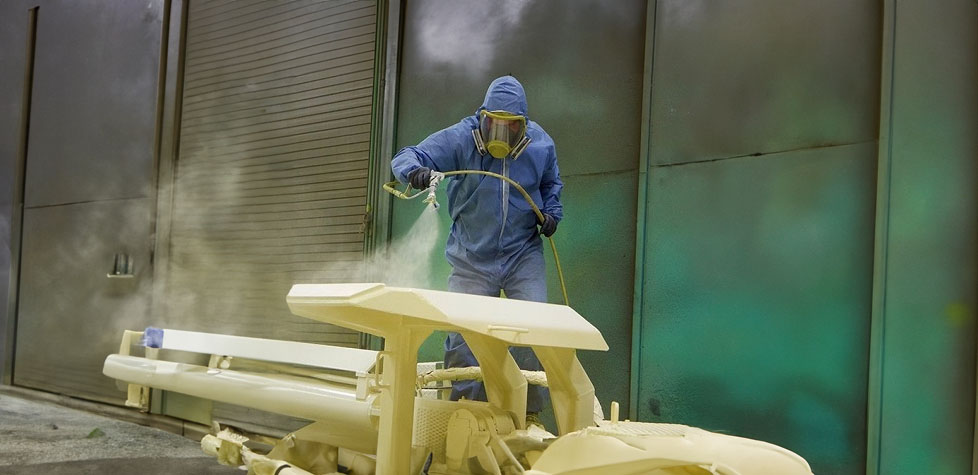
Da Redação –
A proteção contra corrosão de metais e ligas depende de diferentes medidas de proteção, incluindo o uso de revestimentos orgânicos. Atualmente, existe uma infinidade de revestimentos resistentes à corrosão, com base em formulações complexas de agentes formadores de filmes, pigmentos e extensores, aditivos e plastificantes, visando alto desempenho e durabilidade de estruturas expostas a condições adversas.
No entanto, pode ocorrer degradação do revestimento após a exposição. A entrada de água e eletrólitos do ambiente circundante através de poros, rachaduras e outros defeitos pode resultar na perda de proteção contra corrosão dos revestimentos de primer. No caso de camadas de acabamento, a exposição adicional à radiação UV, oxigênio e temperatura pode levar à degradação da matriz polimérica. Portanto, a pesquisa sobre a corrosão ou degradação dos revestimentos é vital para a sua aplicação.
Nas últimas duas décadas, novos materiais, como partículas de nano óxido, hidróxidos duplos em camadas, materiais à base de grafeno, cápsulas poliméricas e esferas, foram utilizados para o des...