A conformidade dos vidros de segurança automotivos
Redação
Para os vidros dos para-brisas há uma legislação do Conselho Nacional de Trânsito (Contran) que exige que sejam utilizados vidros laminados. Ele possui duas lâminas de vidro e uma película entre os vidros. Ao receber qualquer impacto, o vidro não vai estilhaçar. Os fragmentos vão ficar presos a essa película, garantindo a segurança do condutor. No caso do vidro temperado, ele tem uma resistência mecânica maior e, quando se quebra, estilhaça em pequenos pedaços. Dessa forma, deve-se conhecer os requisitos aplicados a materiais de vidro de segurança automotivo utilizados em para-brisas ou outras lâminas, em veículos de categorias M1, M2, M3, N1, N2 e N3, e os respectivos métodos de ensaio para sua avaliação.
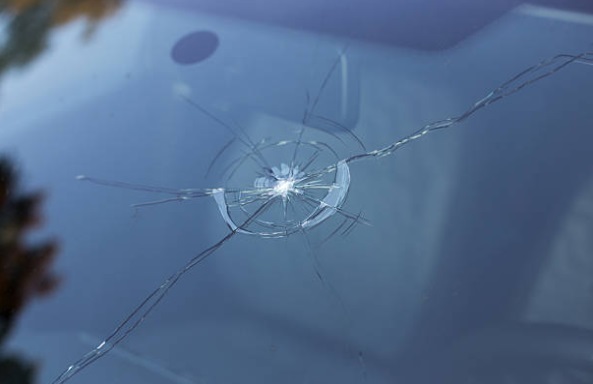
Em uma definição geral, pode-se dizer que o vidro é um produto inorgânico, de fusão, que foi resfriado até atingir a rigidez, sem formar cristais. Na indústria automotiva é utilizado vidro plano e, basicamente, tem-se dois tipos: laminado e temperado. O vidro laminado é utilizado na fabricação de para-brisas e o vidro temperado na fabricação de janelas laterais e traseiras dos veículos. Desde 1990, tem sido obrigatório equipar automóveis com para-brisas de vidro laminado no Brasil, pois não ocorre estilhaçamento quando quebrados.
Quando se pensa em proteção do automóvel, o vidro desempenha um papel fundamental em mantê-lo seguro, porque diminui o risco de ejeção, protege contra raios solares, melhora a proteção contra roubo e diminui barulho externo. Vidro automotivo é amplamente reconhecido como um fator importante na segurança do carro.
O vidro laminado é considerado de segurança, sendo composto de duas lâminas de vidro fortemente interligadas, sob calor e pressão, por uma camada de PVB (poliv...