A resistência à tração e alongamento dos materiais de impermeabilização
Redação
Na construção civil, de qualquer empreendimento comercial, residencial ou industrial, diversas etapas devem ser planejadas para que a execução se torne segura e eficiente. Um serviço que garante a proteção contra a ação de fatores externos é a impermeabilização que é uma etapa que sempre deve ser considerada desde o planejamento.
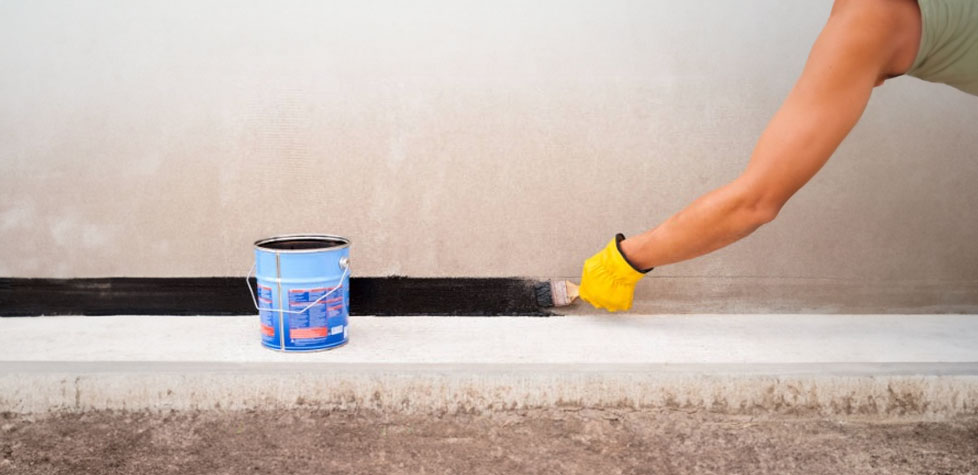
Da Redação –
Normalmente, a vida útil de uma construção é diretamente proporcional à presença da impermeabilização que protege as estruturas contra a ação da água. Ela cumpre a função de formar uma barreira física que impede a propagação da umidade e evita as infiltrações. Assim, previne o aparecimento de manchas de bolor, o desplacamento de azulejos, o surgimento de goteiras e a corrosão das armaduras.
Os impermeabilizantes são usados em praticamente todas as partes da construção, como fundações, subsolos, áreas molháveis, lajes, piscinas, reservatórios, paredes de contenção. As soluções disponíveis no mercado são bastante variadas. No fundo, a impermeabilização na construção civil é um procedimento sistemático empregado com o objetivo de selar, vedar ou colmatar materiais porosos e suas possíveis falhas, geradas por momentos estruturais ou por defeitos técnicos durante a execução.
Sua aplicação é feita com diferentes composições, com a função de evitar a ação das intempéries por meio de infiltrações em qualquer parte da construção — paredes, lajes, aberturas, muros, coberturas, etc. Quand...