A proteção catódica dos dutos terrestres
Redação
Saiba quais são as recomendações para os levantamentos preliminares, projeto, materiais, equipamentos, instalação, pré-operação, operação, inspeção e manutenção de sistemas de proteção catódica para dutos terrestres.
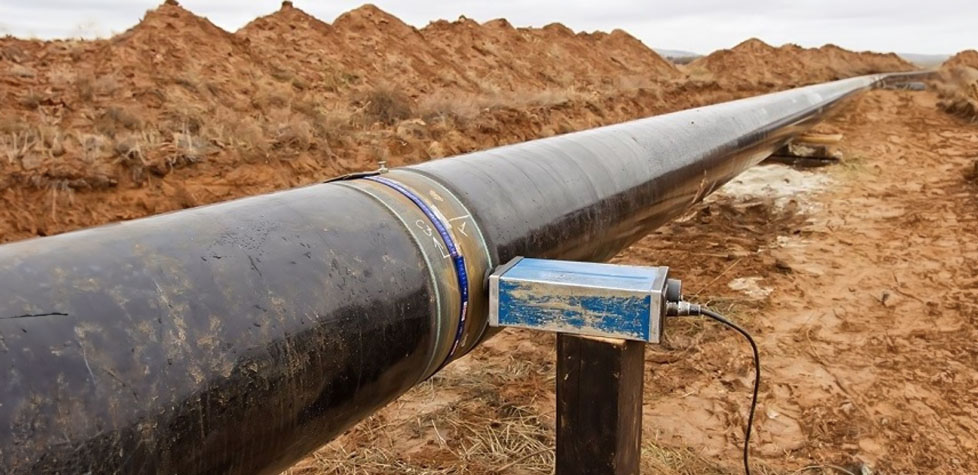
Da Redação -
Os dutos terrestres são usados no transporte de gás, água, derivados de petróleo e minérios, etc. No subsolo, o material está frequentemente exposto a diversos agentes agressivos, como corrosão, interferências elétricas ou influências eletromagnéticas. Caso não exista a proteção adequada, podem ocorrer vazamentos ou outros acidentes que provocam danos às pessoas e ao meio ambiente.
A proteção catódica é um método bastante eficiente para manter a integridade de sistemas enterrados. É uma tecnologia que permite aos engenheiros garantir a proteção contra corrosão. E não somente de instalações no subsolo, mas também daquelas submersas, em especial, na água do mar.
A NBR ISO 15589-1 de 12/2016 - Indústrias de petróleo, petroquímica e gás natural - Proteção catódica de sistemas de transporte por dutos - Parte 1: Dutos terrestres especifica requisitos e fornece recomendações para os levantamentos preliminares, projeto, materiais, equipamentos, instalação, pré-operação, operação, inspeção e manutenção de sistemas de proteção catódica para dutos terrestres, conforme definido na ISO 13623 ou EN 14161, para as indústrias de petróleo, petroquímica e gás natural; e na EN 1594 ou EN 12007-1 e EN 12007-3, usadas pelas indústrias de abastecimento de gás na Europa.