Os conceitos da dureza Brinell
Redação
O ensaio de dureza Brinell consiste em endentar o material com uma esfera de aço endurecido ou metal duro com 10 mm de diâmetro com uma carga de 3.000 kgf. Para materiais mais moles a carga pode ser reduzida para 1.500 kg ou 500 k para reduzir endentação excessiva. A carga total é normalmente aplicada por 10 ou 15 segundos no caso de ferro fundido ou aço e pelo menos durante 30 segundos para outros metais.
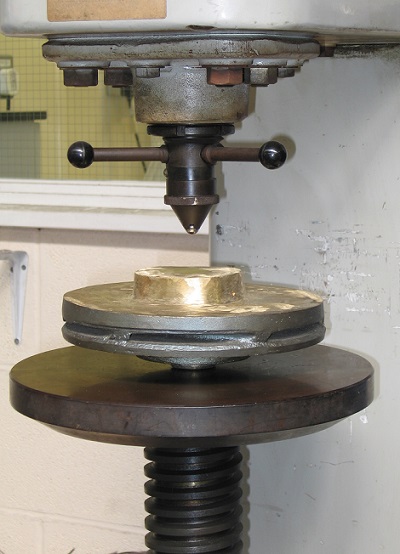
Da Redação –
Em 1900, Johan August Brinell apresentou esse ensaio que passou a ser largamente aceito e depois normalizado, devido à relação existente entre os valores obtidos no ensaio e os resultados de resistência à tração. O ensaio de dureza Brinell consiste em comprimir lentamente uma esfera de aço temperado, de diâmetro D, sobre uma superfície plana, polida e limpa de um metal, por meio de uma carga F, durante um tempo t, produzindo uma calota esférica de diâmetro d. A dureza Brinell é representada pelas letras HB ou Hardness Brinell, que quer dizer dureza Brinell que é a relação entre a carga aplicada (F) e a área da calota esférica impressa no material ensaiado (Ac).
Em resumo, um penetrador (esfera composta de carboneto de tungstênio com diâmetro, D), é pressionado na superfície de um corpo de prova e, após a remoção da força, F, é medido o diâmetro da impressão, d, deixada na superfície. A dureza de Brinell é proporcional ao quociente obtido dividindo a força de ensaio ...