A calibração de sistemas extensométricos usados em ensaios uniaxiais
Redação
O ensaio de tração consiste em aplicar uma força uniaxial no material, tendendo-o a alongá-lo até o momento de sua fratura. Os corpos de prova na maioria das vezes são circulares podendo também serem retangulares. Eles devem ser padronizados por normas técnicas e fixados pelas suas extremidades nas garras de fixação da máquina de tração. São, então, submetidos a um esforço, aplicando uma carga gradativa e registrando cada valor de força correspondente a um diferente tipo de alongamento do material. O ensaio termina quando o material se rompe. Para efeitos de reduzir as diferenças entre as dimensões de diferentes corpos de prova, utiliza-se o conceito de tensão convencional ou tensão de engenharia.
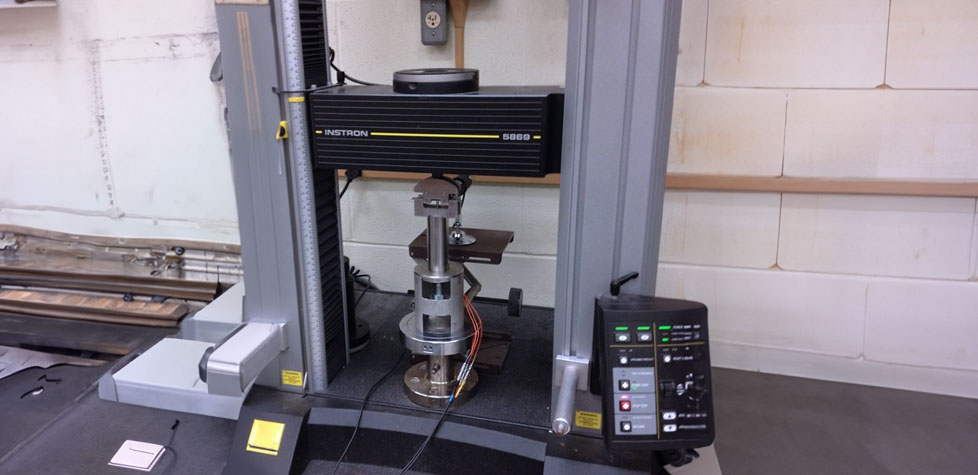
Da Redação –
O ensaio de tração consiste na aplicação de carga de tração uniaxial crescente em um corpo de prova específico até a ruptura. Trata-se de um ensaio amplamente utilizado na indústria de componentes mecânicos, devido às vantagens de fornecer dados quantitativos das características mecânicas dos materiais.
Com esse tipo de ensaio, pode-se afirmar que praticamente as deformações promovidas no material são uniformemente distribuídas em todo o seu corpo, pelo menos até ser atingida uma carga máxima próxima do final do ensaio. Como é possível fazer com que a carga cresça numa velocidade razoavelmente lenta durante todo o ensaio, permite medir satisfatoriamente a resistência do material.
A uniformidade termina no momento em que é atingida a carga máxima suportada pelo material, quando começa a aparecer o fenômeno da estricção ou da diminuição da seção do provete, no caso de matérias com certa ductilidade. A ruptura sempre se dá na região mais estreita do material, a menos que um defeito interno no material, fora dessa região, promova a sua ruptura, o que raramente acontece.
A pr...