Avaliando os riscos em empresas de manufatura
Redação
Uma das principais causas de acidentes, até mesmo fatais, estão relacionados à exposição dos trabalhadores na operação de máquinas nas quais suas partes móveis não dispõem de proteção. Fazer o rastreamento e identificar as máquinas passíveis de gerar danos é imprescindível para aplicação futura de medidas de segurança. Para isso faz-se necessário conhecimento dos equipamentos, bem como das partes móveis nas quais o trabalhador está exposto, para assim definir o tipo de prevenção adequada ao grau do risco identificado. A aplicação de uma ferramenta de apreciação de riscos e cumprir as normas técnicas são vitais para auxiliar na tomada de decisão.
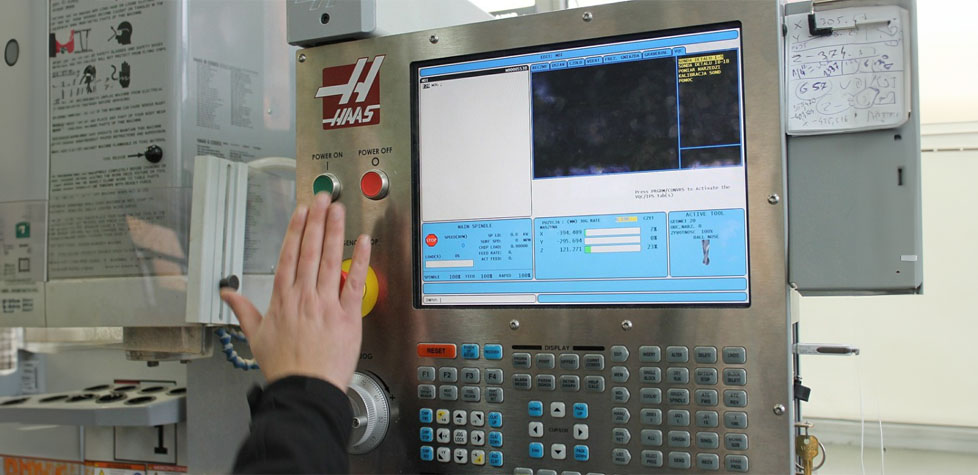
Mauricio Ferraz de Paiva -
O processo de avaliação de riscos ou os elementos de gestão do risco podem ser divididos em uma série de etapas: elaborar um programa de avaliação de riscos no local de trabalho; estruturar a avaliação (decisão sobre a abordagem: geográfica/funcional/ao nível do processo/do fluxo); reunir informação; identificar perigos; identificar as pessoas em risco; identificar padrões de exposição das pessoas em risco; avaliar os riscos (probabilidade de danos/gravidade dos danos nas circunstâncias atuais); analisar opções de eliminação ou de controlo dos riscos; priorizar as ações a implementar e definir medidas de controlo; implementar controles; registrar a avaliação; medir a eficácia das medidas aplicadas; rever (sempre que se verifiquem alterações, ou periodicamente); e monitorar o programa de avaliação de riscos.
Para a maioria das empresas, especialmente as pequenas e médias empresas, uma abordagem direta, dividida em cinco etapas, poderá funcionar bem:
Etapa 1. Identificação dos perigos e das pessoas em risco – Análise dos aspectos do trabalho que podem causar danos, e identificação dos trabalhadores que podem estar expostos ao perigo.
Etapa 2. Avaliação e priorização dos riscos – Apreciação dos riscos existentes (gravidade e probabilidade dos potenciais danos…) e classificação desses riscos por ordem de importância.
Etapa 3. Decisão sobre medidas preventivas – Identificação das medidas adequadas...