Os métodos de ensaio de tubos de polietileno para transporte de fluidos
Redação
Entre as vantagens do tubo de polietileno, algumas se destacam. Oferecem uma maior variedade de diâmetros e classes de pressão, tem alta resistência química, à abrasão e impactos. São imunes à corrosão, possui baixo efeito de incrustação e baixa rugosidade. Caracterizado por sua soldabilidade e atoxidade, são de fácil manuseio e instalação, sendo mais leves e flexíveis que os tubos comuns e possuem uma boa vida útil e excelentes características hidráulicas. Conheça os requisitos e métodos de ensaio para fabricação e recebimento de tubos de polietileno para transporte de fluidos em temperaturas de até 40 °C, com máxima pressão de operação de até 2,5 MPa, projetados para vida útil de 50 anos.
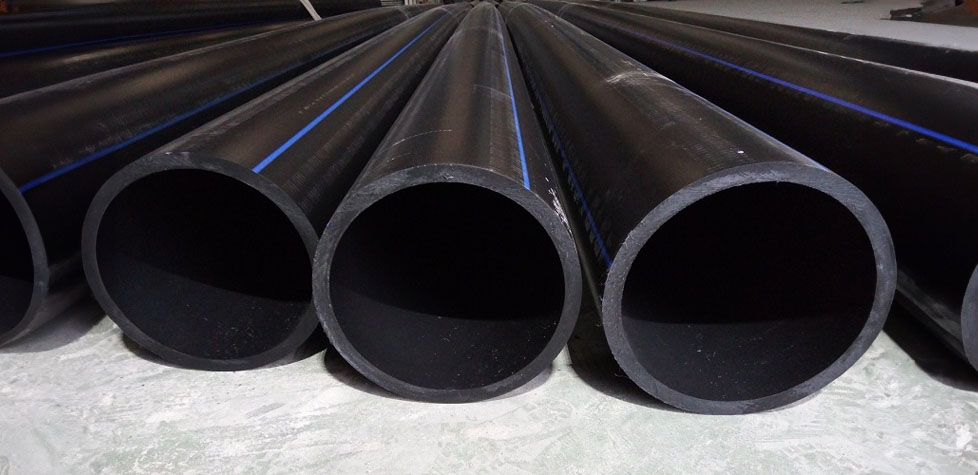
Da Redação –
A tubulação de polietileno é uma solução eficaz quanto aos custos para a resolução de uma ampla gama de problemas urbanos, industriais, marítimos, mineração, aterros e aplicações agrícolas. Sua eficácia foi testada e comprovada para diversas aplicações de superfície, enterrado, instalações marítimas, flutuantes e submersas.
Em função da sua flexibilidade – diâmetros de até 125 mm são fornecidos em bobinas e acima de 125 mm, em barras de 6, 12 ou 18 metros – sua instalação requer valas muito menores, proporcionando uma redução significativa no custo. A tubulação em polietileno permite ainda que sua instalação também seja feita pelo método não destrutivo.
A tubulação de polietileno de alta densidade pode ser utilizada em linhas de água potável, águas residuais, lamas, produtos químicos, resíduos perigosos e gás comprimido. Na verdade, a tubulação de polietileno tem uma longa e distinta história de serviço aos setores de gás, petróleo, mineração e outras indústrias. Possuem a mais baixa frequência de reparos por quilômetro/ano em comparação com todos os demais materiais utilizados...