Os ensaios em vidros revestidos para controle solar
Redação
Essa tecnologia mostra uma tendência da indústria por maior eficiência energética dos edifícios. O material começou a ser utilizado no Brasil por volta da década de 80, quando era chamado de vidro refletivo. Com a busca por sustentabilidade no setor somada à evolução da tecnologia de metalização do vidro, o processo permitiu a fabricação de produtos menos refletivos e, consequentemente, mais transparentes.
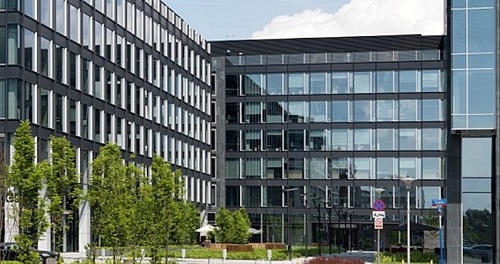
Da Redação –
Em sua fabricação, nesse tipo de vidro, os revestimentos exercem grande domínio sobre as propriedades térmicas e viabilizam soluções diversas, caracterizadas genericamente como vidros seletivos. A equação consiste em adequar a relação entre transmissão luminosa (luz visível) e fator solar (energia transmitida e absorvida). Assim, o processo busca obter um vidro capaz de conciliar os dois aspectos mais desejados pela arquitetura brasileira atualmente: alta transmissão de luz e baixo ganho de calor.
Os vidros com controle solar proporcionam benefícios energéticos às edificações, reduzindo o consumo de eletricidade, pois tornam menos necessário o uso de sistemas de climatização e iluminação artificiais. O produto é indicado para fachadas de edifícios, mas pode não ser a melhor opção quando se quer visuais mais transparentes.
A diferença entre o vidro de controle solar e o vidro comum é o revestimento metalizado em sua superfície, também chamado de coating, que confere suas propriedades. Essa camada metalizada pode ter características bem distintas, que serão de grande importâ...